CFD Simulation of ‘Spray Dryer’ System
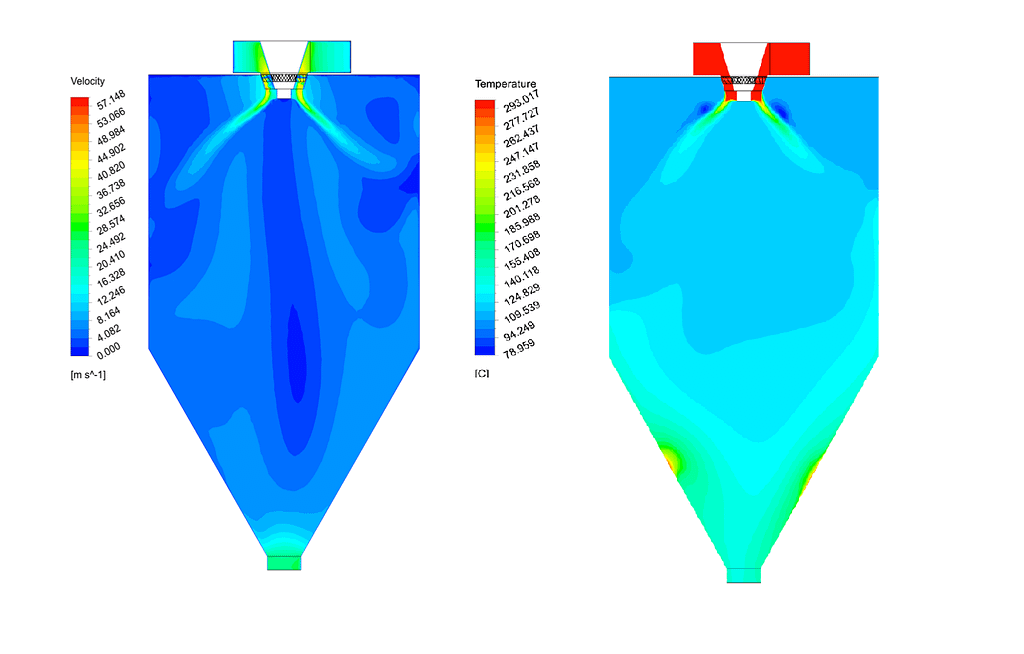
Producing this powder with a well-controlled particle size distribution as well as particle shape, structure and appearance is of main interest for Food and Pharma industry.
The principal governing factors which determining the final size and shape of the particles in the powder product, is initial droplet size, droplet trajectory along with its variables such as velocity, contact angle and moisture content.
The atomized droplets inevitably collide with each other, which leads to a continuous evolution of the particle size and structure that cause significant change in the final particle size and structure.
At Fluent Engineering Solutions, we have simulated and designed multiple spray dryer systems which include co-current, counter current, atomiser type, nozzle type, spin flash dryer, paddle dryer and Integrated fluidised bed spray dryers.
CFD enables you to visualise confirm the predicted particle flow pattern along with the all droplet properties associated with it. This information is extremely significant to modify air distributor, nozzle cone angle, diameter, height of the chamber, agglomeration or wall drifting possibilities.
You can start to build virtual prototype which is already in sales and design phase. Using CFD simulation results we can test and verify several design concept and evaluate the performance of proposed design even before the plant has been built.